Materials Used for Rubber Molding
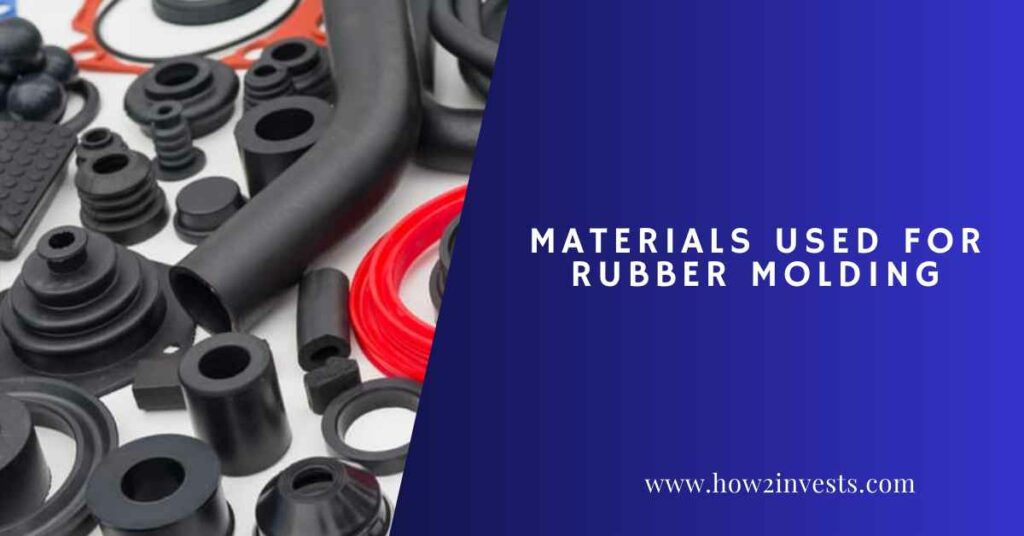
Rubber’s basic structure is adaptable, allowing for the creation of several variations with unique qualities.
Manufacturers can transform these raw materials into durable, high-quality products using specialized molding machinery. Here are some common rubber molding materials:
Table of Contents
Polyisoprene (IR)
Polyisoprene, or isoprene rubber (IR), is a product of synthetic isoprene polymerization. It exhibits some physical and chemical characteristics of natural rubber but is lighter in color, more homogeneous, and more pure.
It can be either stiff and leatherlike or soft and flexible, depending on the chemical structure. IR works best for molds like bearings and seals, which require a rigid, high-purity material with high tensile strength and tear resistance.
Styrene-Butadiene Rubber (SBR)
The polymerization of styrene and butadiene produces styrene-butadiene rubber (SBR), a multipurpose synthetic rubber.
This polymer has exceptional abrasion resistance, high impact strength, and age stability with the correct additions. SBR offers a cost-effective solution for wear-resistant, high-strength, and non-toxic rubber molding, such as drive couplings.
Ethylene-Propylene (EPM & EPDM)
Ethylene-propylene rubbers have excellent electrical insulation qualities and resistance to ozone, high temperatures, sunshine, and weathering.
EPDM may be used outside for lengthy periods without degradation. These molding materials also resist polar fluids like alcohol, alkalis, acids, steam, and coolant. Common EPM and EPDM applications include automotive moldings and seals.
Nitrile Rubber (NBR)
Acrylonitrile and butadiene combine to form nitrile rubber or acrylonitrile-butadiene rubber (NBR). The more acrylonitrile manufacturers use in the composition of this substance, the more resistance it offers to petroleum-based oils and fuels.
Nitrile rubber has high tensile strength, a low compression set, and high stability over a broad temperature range. Nitrile-based rubbers are well-suited for automotive, aerospace, and industrial applications, including creating O-rings, static seals, and oil seal molding.
Silicone
The transparent silicon material is made of siloxane. Due to its flexibility, silicone is excellent for custom-molded shapes and applications with specific requirements.
The material can acquire water and temperature resistance by slightly altering the compound recipe. Silicon molds can be made in any color, making them popular for creative models and testing by design engineers.
Silicone maintains a low compression set and flexibility in extreme temperatures. It also provides excellent electrical insulation and flame resistance. These characteristics make silicone a great sealing material for various applications and industries.
Thermoplastic Elastomers (TPE)
Thermoplastic elastomer (TPE) is a flexible material that behaves like plastic. It combines hard segments that provide strength and resistance with soft ones that increase flexibility.
These properties enable the material to be heated up similarly to plastic while preserving rubber-like elastic properties after.
Extrusion, injection, and blow molding are plastic production tools that process thermoplastic elastomers. TPE can be used in advanced processing like two-shot molding and overmolding.
They allow for flexible part design and easy bonding to other thermoplastic substrates. Sealings, gaskets, and O-rings are typical applications for injection-molded TPEs.
Considerations For Rubber Molding Material
When choosing rubber molding material, balance between cost, compatibility, and manufacturability. It should be capable of withstanding surrounding conditions, such as humidity, temperature, chemicals, and sunshine exposure.
The material should also produce the desired product while preserving its beneficial features. Contact a reputable rubber and plastic manufacturing company to find quality molding.